Disc Anode
Efficient electrochemical process
Easy installation
Low maintenance
- Product Description
Product Introduction
Welcome to our dedicated page for the Disc Anode, a revolutionary product designed for high-performance electrochemical applications. At Shaanxi Tianyi New Material Titanium Anode Technology Co., Ltd., we specialize in the production of advanced titanium anodes, and our product is at the forefront of our product range. Engineered for durability and efficiency, this anode is essential for a variety of industries, including water treatment, industrial electroplating, and cathodic protection.
Product Specifications
Substrate | Titanium Gr1 |
Coating | Iridium Oxide (IrO2), Ruthenium Oxide (RuO2), Tantalum Oxide (Ta2O5) |
Shape | Disc or Disk |
Diameter | φ25, φ60, φ100, φ150, |
Application | water tanks, Pressure Vessels, Oil and Gas Pipeline, Vessels |
Design Life | Specified 20-100 years |
Environment | Seawater environments/Marine Structures |
![]() | ![]() |
![]() | ![]() |
Product Composition and Design
The product is crafted from high-grade titanium alloy, featuring a robust MMO coating that enhances its performance in electrochemical processes. The innovative design ensures a uniform surface area, facilitating consistent current distribution and maximizing efficiency. Our customization options allow clients to specify dimensions and coating types, making the Disc Anode suitable for various applications.
Product Advantages
- High Corrosion Resistance: The titanium alloy and MMO coating provide exceptional resistance to corrosion, extending the anode's lifespan.
- Enhanced Performance: Designed for optimal current distribution, our product maximizes efficiency and reduces energy consumption.
- Customizable Options: Tailor the anode to your specific needs with various sizes and coatings available.
- Environmentally Friendly: Our products promote sustainable practices, supporting eco-friendly industrial processes.
Technical Features
- Electrochemical Stability: Maintains performance under diverse conditions, ensuring reliability in demanding environments.
- High Current Density: Capable of supporting high current loads, making it ideal for large-scale applications.
- Lightweight: The titanium construction makes it easy to handle and install.
Product Application
The Disc Anode is widely used across various sectors, including:
Marine Structures: MMO disc anodes are widely used to protect marine structures such as ship hulls, docks, piers and offshore platforms. They counteract the corrosive effects of seawater on these structures.
Storage Tanks: They can be used on the bottom of above-ground storage tanks, on the outside of underground tanks to prevent corrosion.
Pipelines: MMO disc anodes are used to protect both onshore and offshore pipelines, ensuring they are protected from corrosion throughout their service life.
Water Treatment Facilities: They are also used in water treatment plants and desalination facilities to protect equipment from corrosive elements in the water.
Reinforced Concrete Structures: MMO disc anodes can be used to protect the steel reinforcement within concrete structures, preventing corrosion of the steel, thereby extending the service life of the structure.
Cooling Systems: In industrial cooling systems, MMO disc anodes can help protect infrastructure from the corrosive effects of coolants.
Electrochlorination Systems: They play a role in the production of chlorine from salt water, a process called electrochlorination.
Heat Exchangers: They can be used to protect heat exchangers from the corrosive effects of the fluids they handle.
Be used in a wide range of industries.
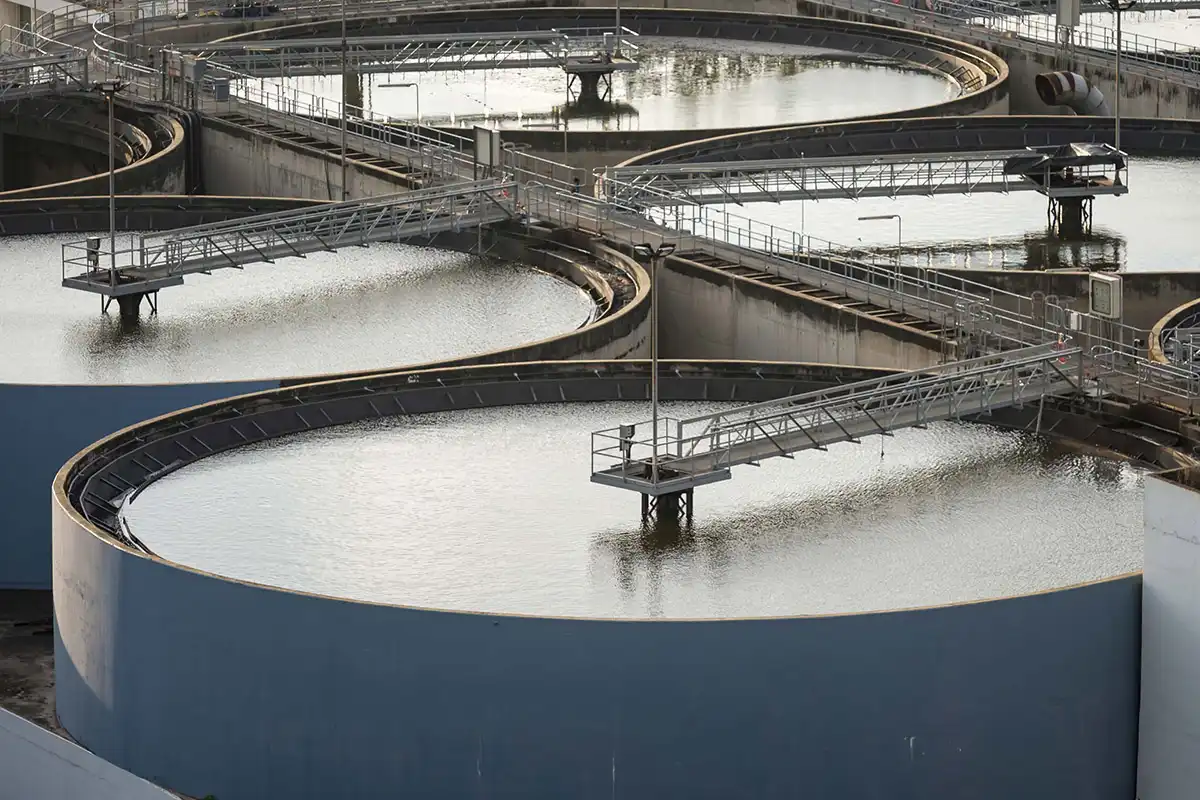
Water treatment
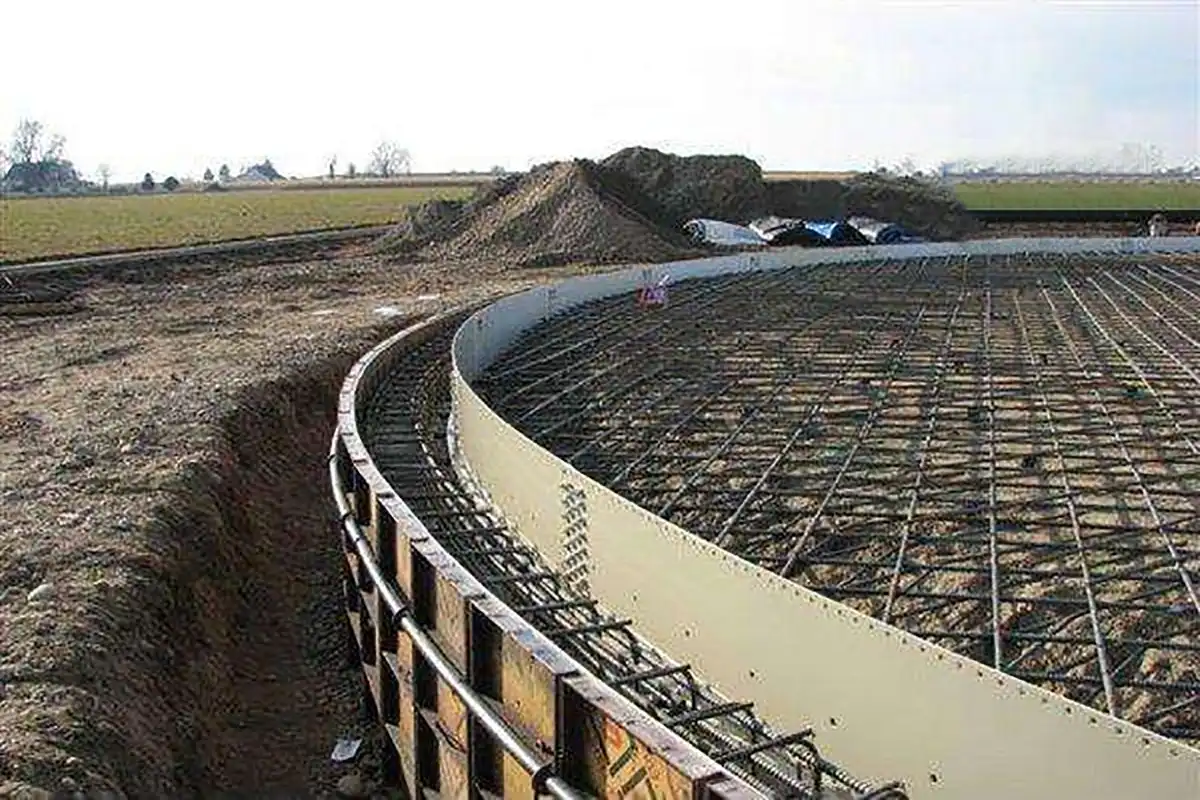
Cathodic protection of oil tank bottom plate
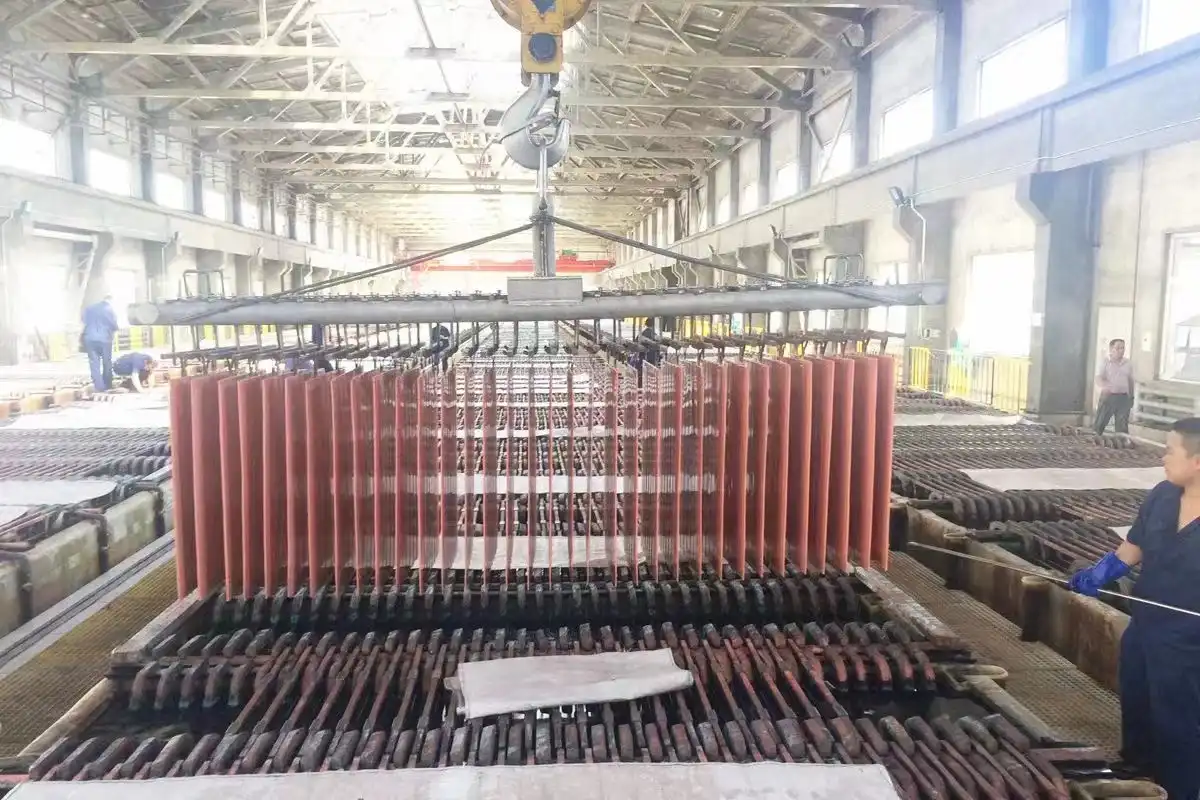
Aluminum foil manufacturing industry
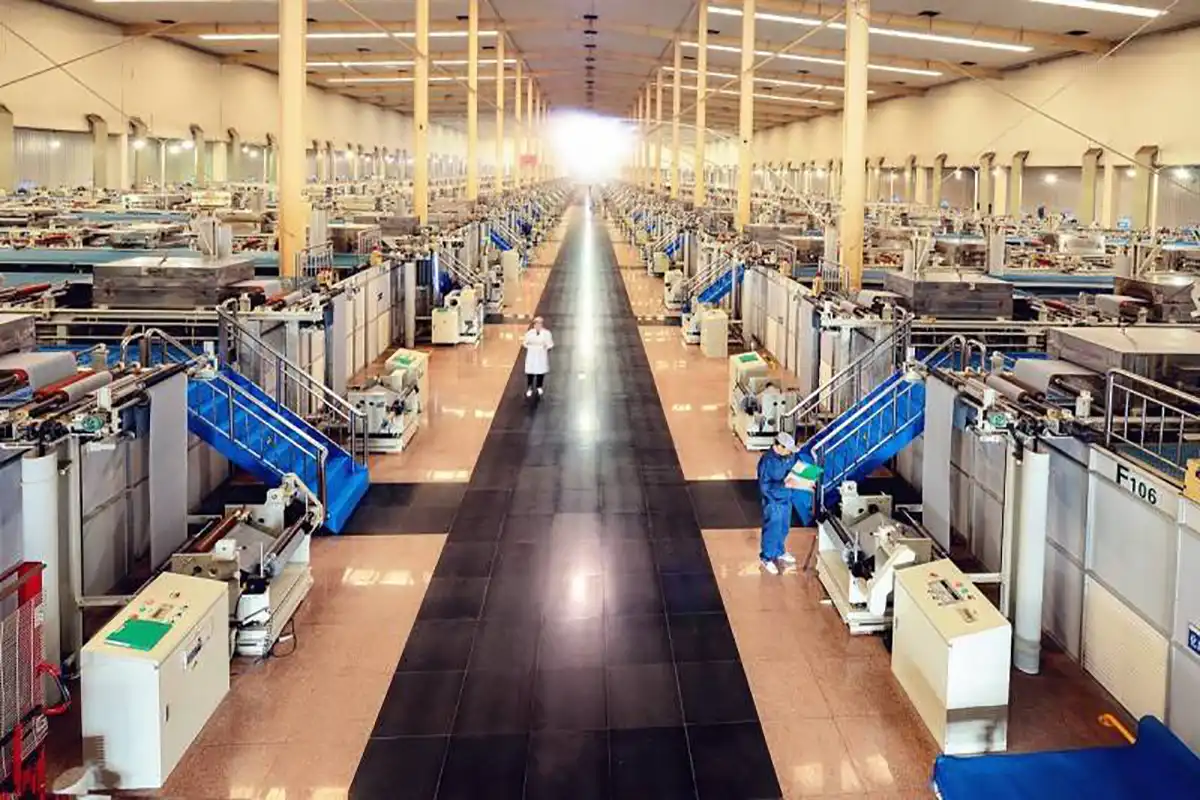
Copper foil manufacturing industry
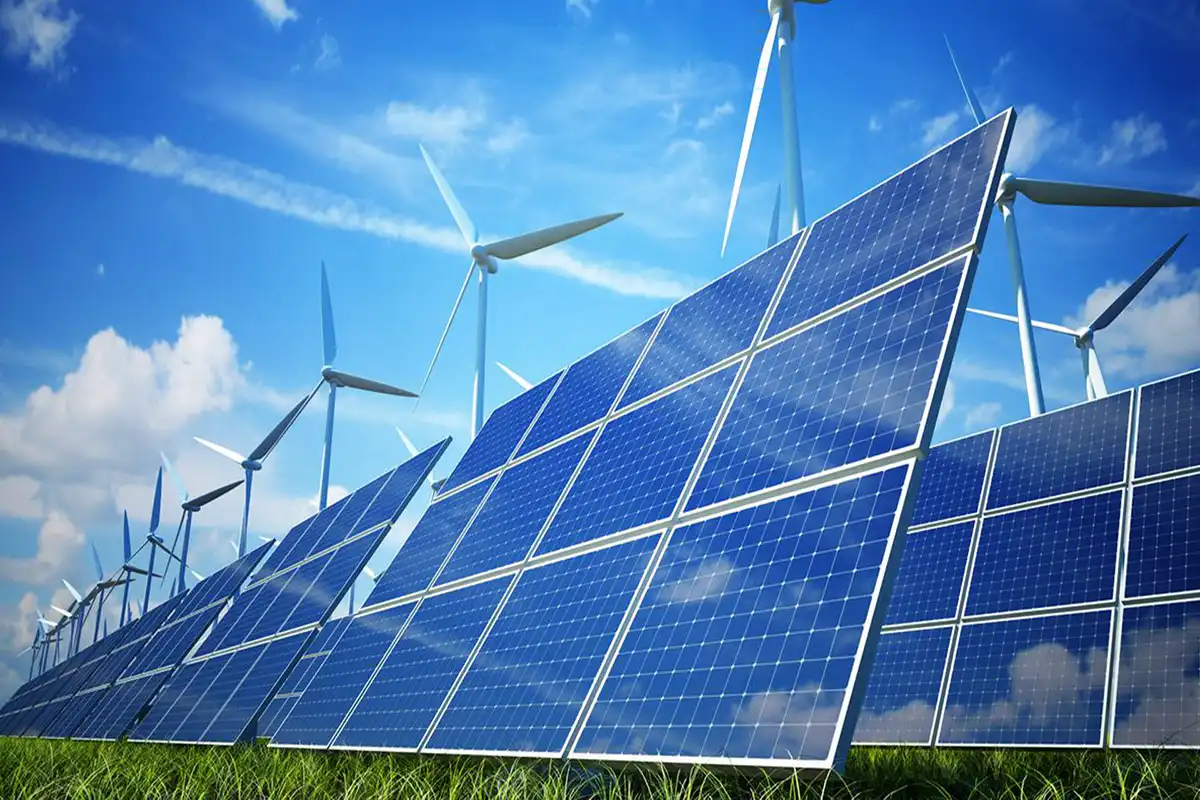
Energy industry
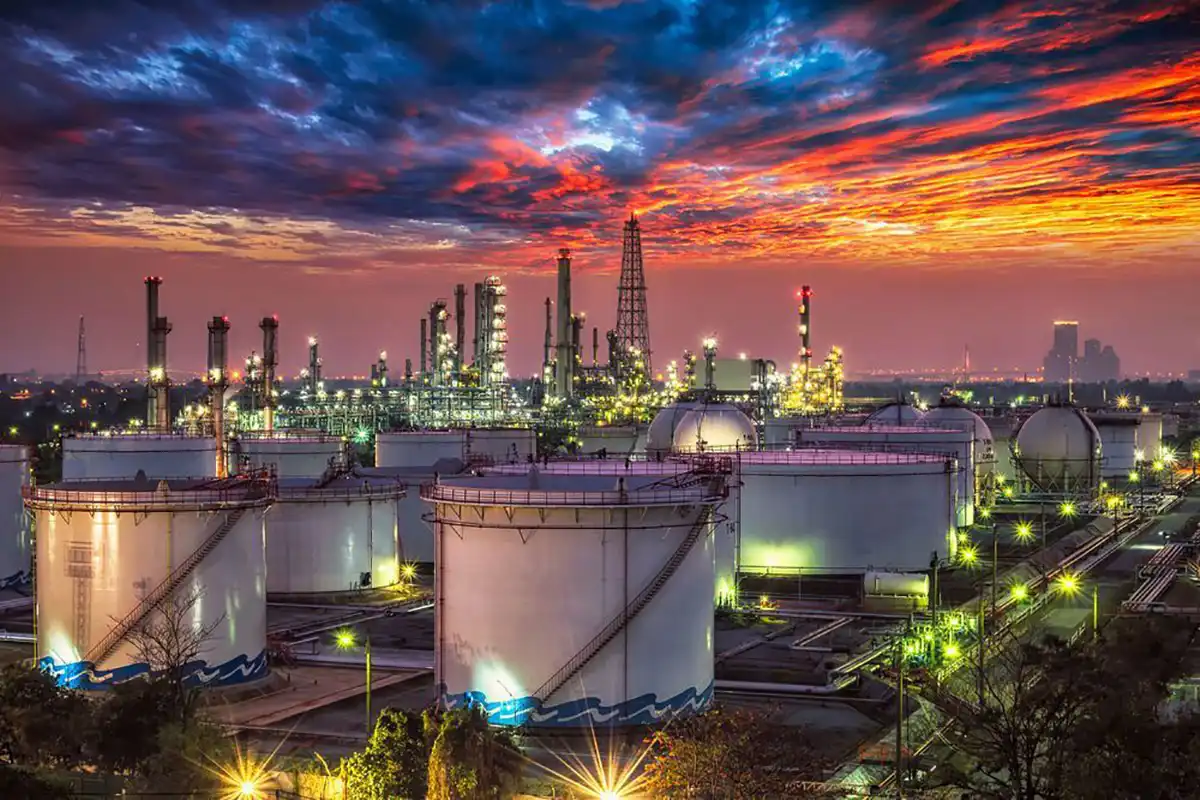
Chemical industry
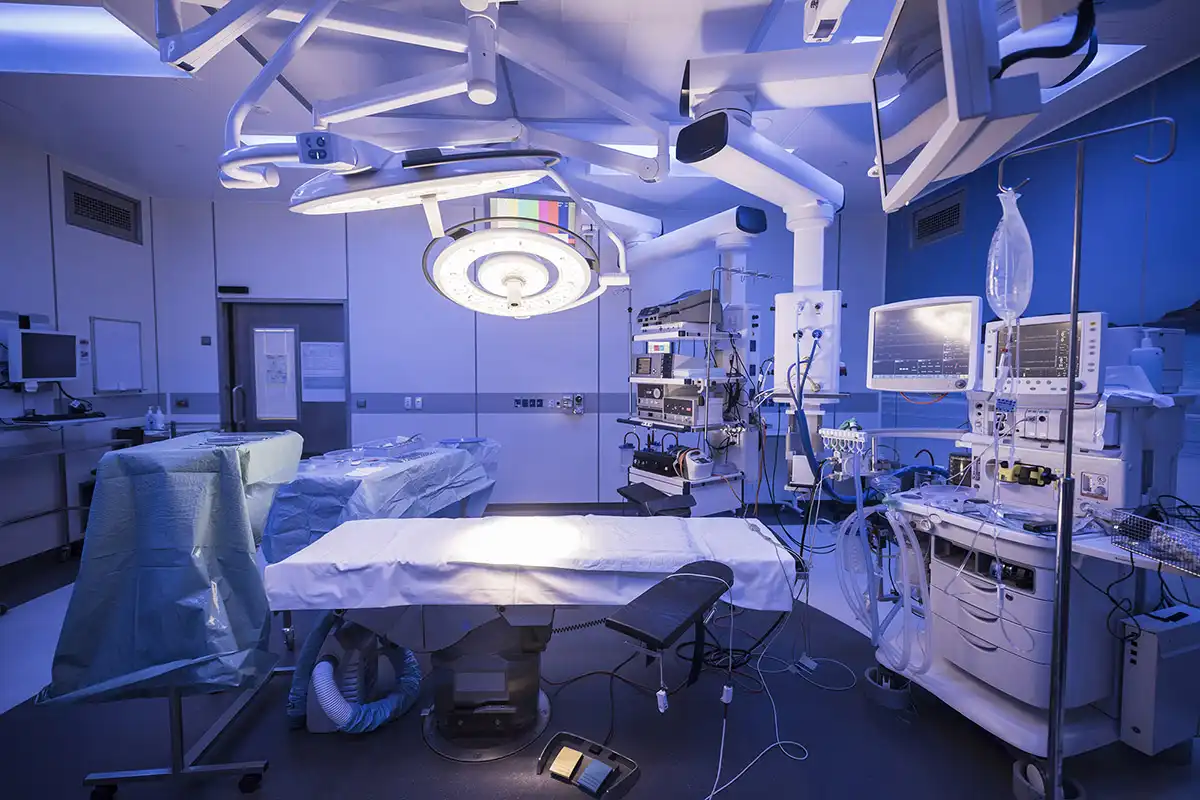
Medical equipment
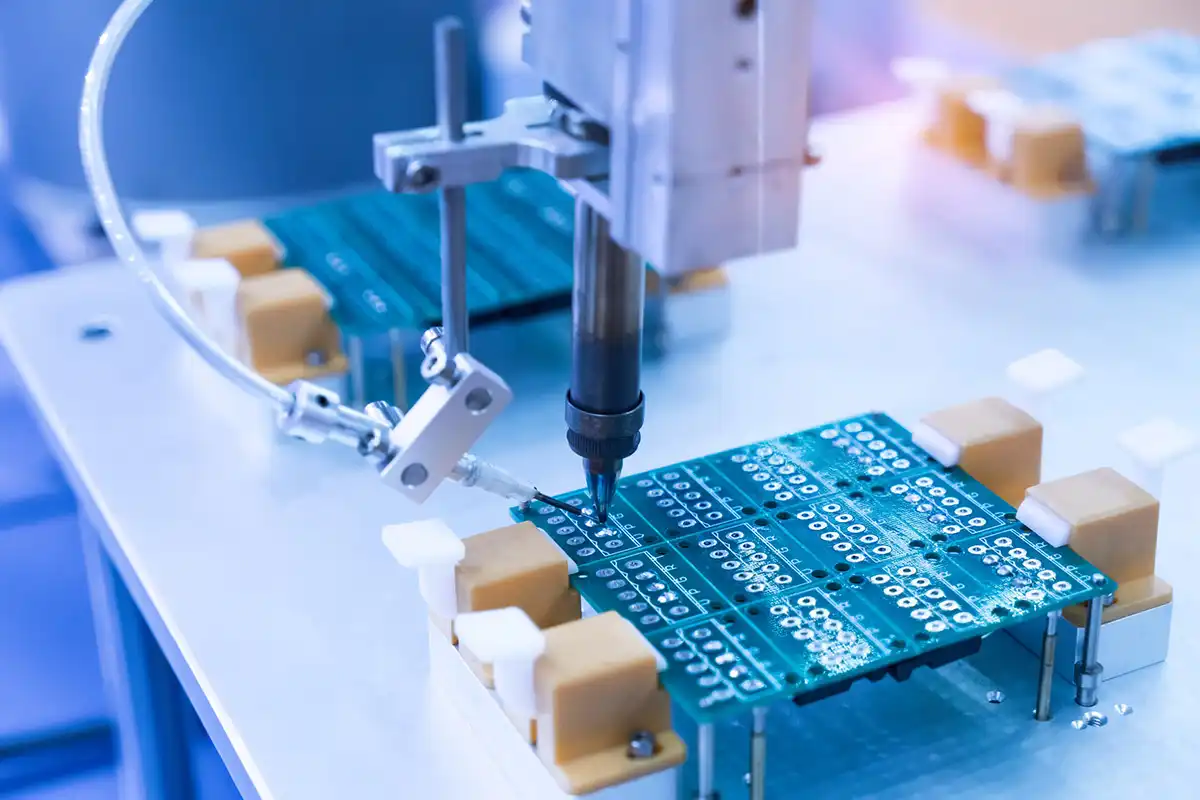
Electronic plating
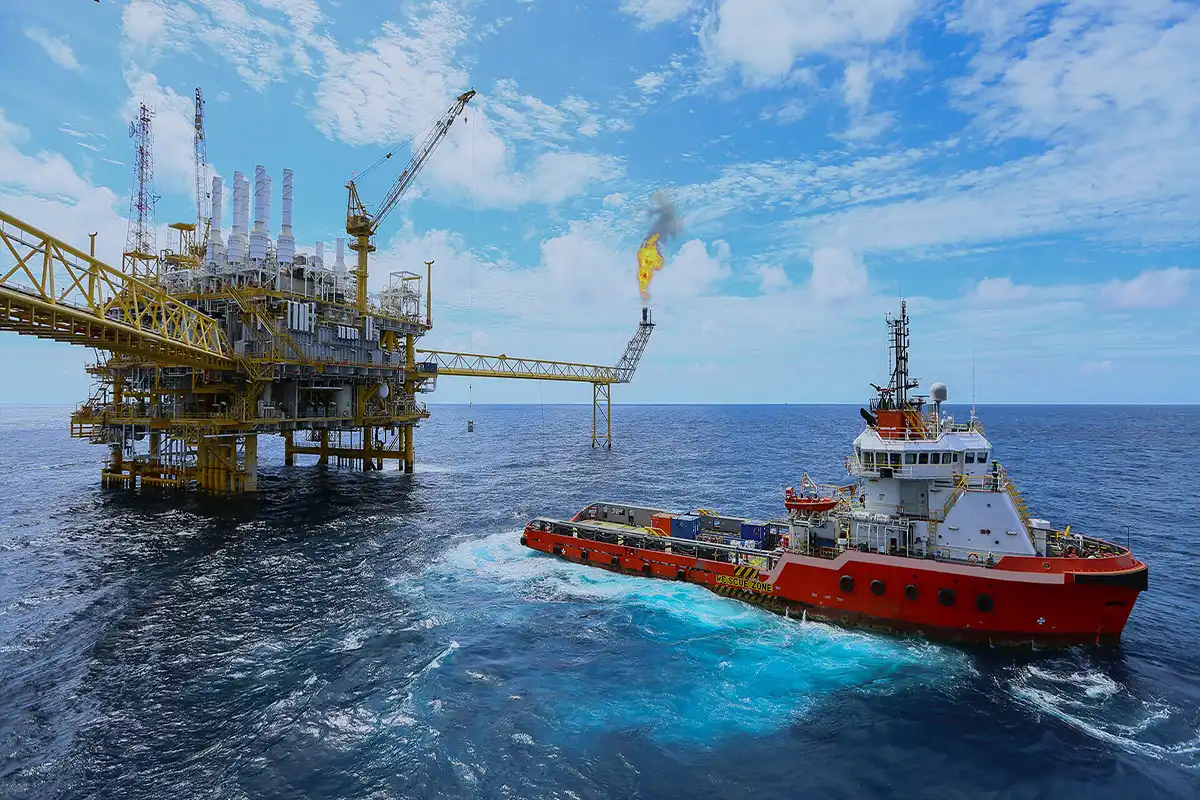
Marine engineering
Our Workshop
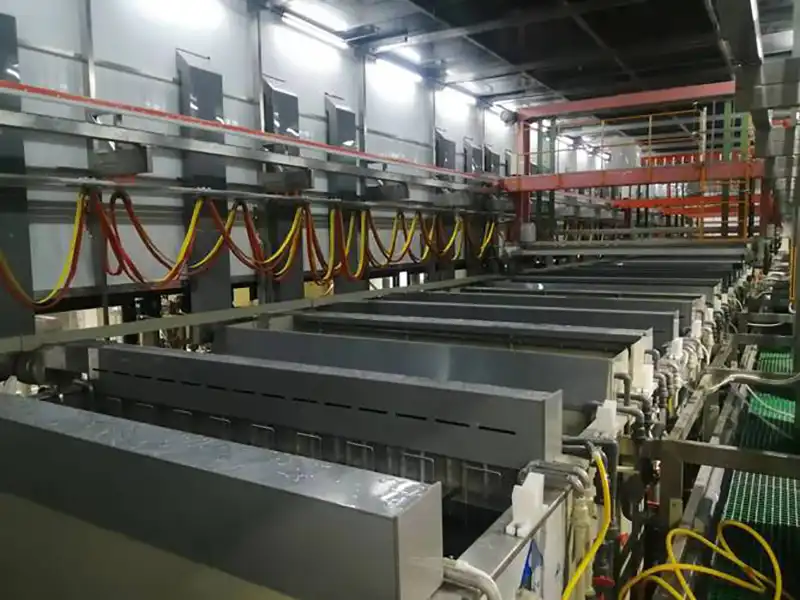
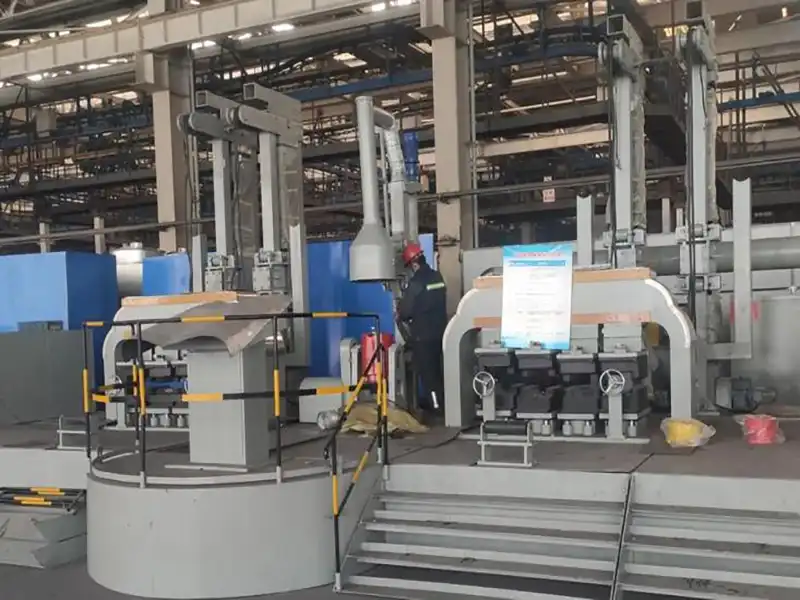
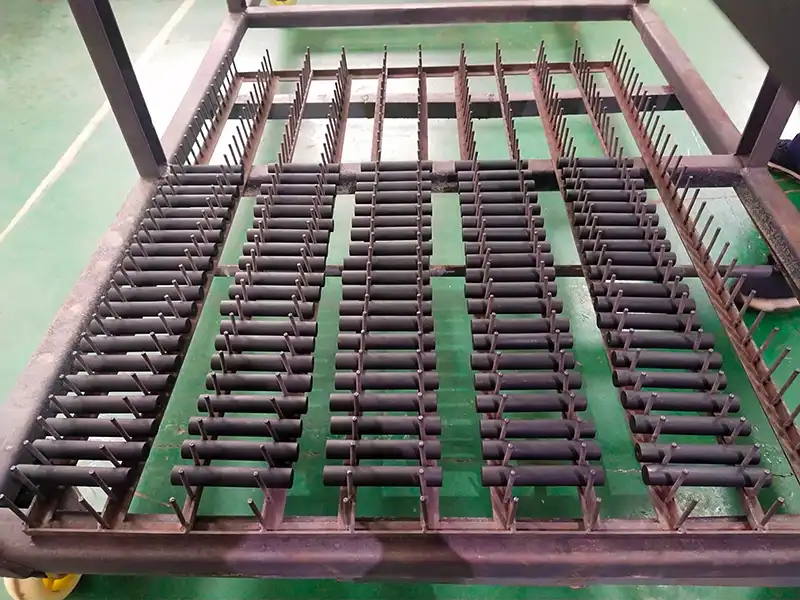
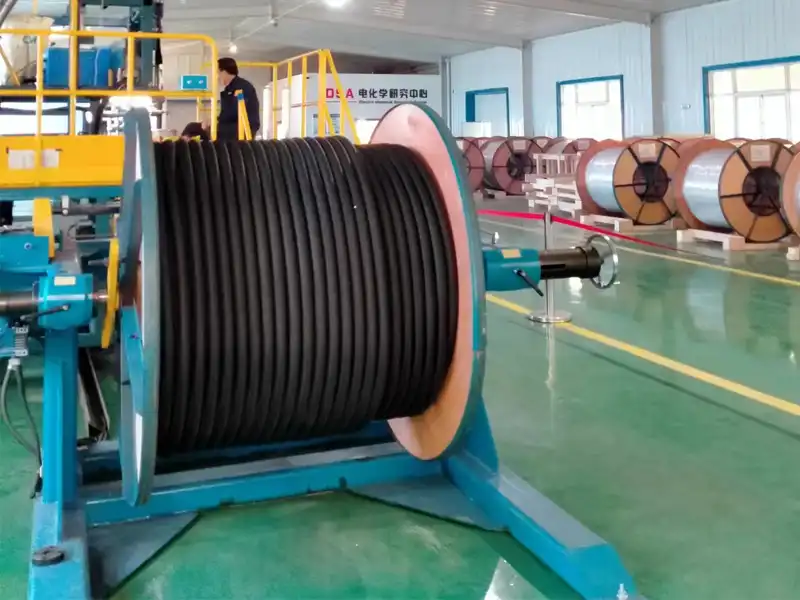
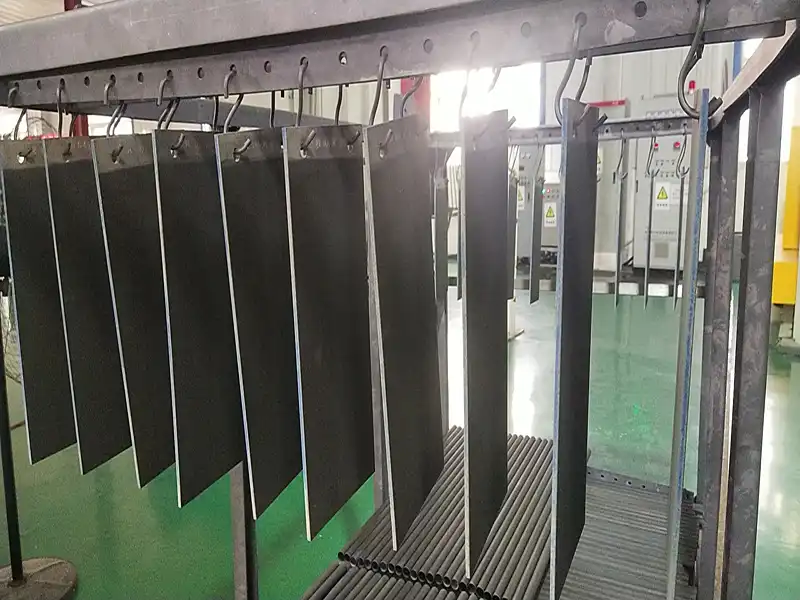
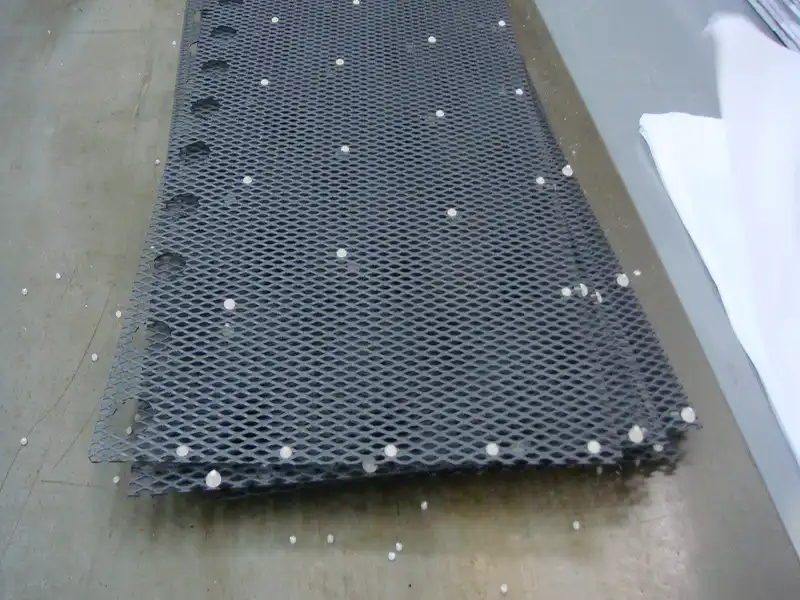
Product Production Process
Our products are manufactured using state-of-the-art technology, ensuring precision and quality at every stage. The production process includes:
Material Selection
The production of disc anodes begins with the careful selection of suitable materials. Commonly, high-grade titanium is chosen for the substrate due to its excellent corrosion resistance and mechanical strength, which are crucial for longevity in electrolytic environments.
Cutting and Shaping
Titanium plates are precisely cut into disc shapes using advanced techniques such as laser cutting or water jet cutting. This process ensures that each disc adheres to the specified dimensions and thickness, optimizing their performance for electrochemical applications.
Surface Preparation
The surface of each titanium disc undergoes extensive cleaning and treatment to enhance adhesion for the subsequent coating. This may involve processes such as acid etching, sandblasting, or abrasive cleaning to remove any impurities or oxides from the surface.
Coating Preparation
A coating solution is prepared, often consisting of mixed metal oxides such as iridium oxide, ruthenium oxide, or other suitable compounds. The selected metal oxides are dissolved in a solvent to create a homogenous mixture ready for application.
Coating Application
The coating is applied to the titanium discs using techniques like dip coating, spray coating, or electrochemical deposition. This step is critical for forming a uniform and adherent coating that enhances the electrochemical activity of the anode.
Curing Process
After the coating application, the discs undergo a curing process, typically involving heating to specific temperatures. This process promotes the bonding of the oxide layer to the titanium substrate, ensuring durability and enhanced performance.
Quality Control
Each production batch of disc anodes is subjected to stringent quality control tests. This includes evaluating coating thickness, adhesion strength, and electrochemical performance to ensure compliance with established standards.
Final Inspection
Before packaging, the disc anodes undergo a thorough final inspection to check for any defects in dimensions, surface quality, and overall consistency. This step is vital to ensure that only top-quality products are shipped to customers.
Packaging
The finished disc anodes are carefully packaged using protective materials to prevent any damage during transport. Each package is labeled with detailed product specifications, including size, material, and intended use.
Documentation
Accompanying the disc anodes is comprehensive documentation that includes product specifications, installation guidelines, and safety information. This ensures that customers have all necessary information for proper handling and usage.
Shipping
Finally, the packaged disc anodes are shipped to customers via reliable logistics partners. Tracking systems are implemented to monitor the delivery process and ensure timely receipt by the customers.
By following this detailed production process, disc anodes are created with a focus on quality and performance, making them suitable for various applications in electrochemistry, water treatment, and industrial processes.
Material Selection
The production of disc anodes begins with the careful selection of suitable materials. Commonly, high-grade titanium is chosen for the substrate due to its excellent corrosion resistance and mechanical strength, which are crucial for longevity in electrolytic environments.
Cutting and Shaping
Titanium plates are precisely cut into disc shapes using advanced techniques such as laser cutting or water jet cutting. This process ensures that each disc adheres to the specified dimensions and thickness, optimizing their performance for electrochemical applications.
Surface Preparation
The surface of each titanium disc undergoes extensive cleaning and treatment to enhance adhesion for the subsequent coating. This may involve processes such as acid etching, sandblasting, or abrasive cleaning to remove any impurities or oxides from the surface.
Coating Preparation
A coating solution is prepared, often consisting of mixed metal oxides such as iridium oxide, ruthenium oxide, or other suitable compounds. The selected metal oxides are dissolved in a solvent to create a homogenous mixture ready for application.
Coating Application
The coating is applied to the titanium discs using techniques like dip coating, spray coating, or electrochemical deposition. This step is critical for forming a uniform and adherent coating that enhances the electrochemical activity of the anode.
Curing Process
After the coating application, the discs undergo a curing process, typically involving heating to specific temperatures. This process promotes the bonding of the oxide layer to the titanium substrate, ensuring durability and enhanced performance.
Quality Control
Each production batch of disc anodes is subjected to stringent quality control tests. This includes evaluating coating thickness, adhesion strength, and electrochemical performance to ensure compliance with established standards.
Final Inspection
Before packaging, the disc anodes undergo a thorough final inspection to check for any defects in dimensions, surface quality, and overall consistency. This step is vital to ensure that only top-quality products are shipped to customers.
Packaging
The finished disc anodes are carefully packaged using protective materials to prevent any damage during transport. Each package is labeled with detailed product specifications, including size, material, and intended use.
Documentation
Accompanying the disc anodes is comprehensive documentation that includes product specifications, installation guidelines, and safety information. This ensures that customers have all necessary information for proper handling and usage.
Shipping
Finally, the packaged disc anodes are shipped to customers via reliable logistics partners. Tracking systems are implemented to monitor the delivery process and ensure timely receipt by the customers.
By following this detailed production process, disc anodes are created with a focus on quality and performance, making them suitable for various applications in electrochemistry, water treatment, and industrial processes.
Quality Inspection
Quality is our top priority. Every Disc Anode undergoes rigorous testing throughout the production process, from raw material inspection to final product evaluation. Our commitment to excellence ensures that each anode meets the highest performance benchmarks.
Packaging Method
We employ custom packaging solutions designed to protect the anodes during transit. Our packaging methods include:
- Protective Wrapping: Safeguarding against physical damage.
- Moisture-Proof Materials: Ensuring long-term integrity.
- Eco-Friendly Options: Supporting sustainable practices through recyclable materials.
![]() | ![]() | ![]() |
Our Certificates
Our Team
![]() | ![]() |
OEM Service
Shaanxi Tianyi offers comprehensive OEM services, providing tailored solutions that meet the unique needs of our partners. Whether you require specific coatings, sizes, or packaging options, we are here to deliver high-performance products that align with your requirements.
FAQ
Q: What is the lifespan of a product?
A: The product typically lasts over 5 years, depending on the application and operating conditions.
Q: Can I customize the size of the product?
A: Yes, we offer a range of customizable sizes to fit your specific needs.
Q: What industries use te products?
A: Our products are used in water treatment, electroplating, hydrometallurgy, and more.
Contact Us
For more information about our Disc Anode and how it can benefit your applications, please reach out to us at [info@di-nol.com]. Our team is ready to assist you with any questions or custom requests. With our expertise in electrochemical materials and technologies, Shaanxi Tianyi New Material Titanium Anode Technology Co., Ltd. is your trusted partner for high-quality, sustainable solutions. Thank you for considering our products!